Metal
Bending
|
|
|
|
|
|
|
|
|
|
|
|
 |
Chicago Dreis & Krump Hydraulic
and Mechanical Powered Leaf Brake machines with push button controls
to bend metal and fold metal into many shapes including box and pan
shapes.
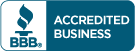
Below you
will see our hydraulic leaf brake machines for bending metal up to 1/4
inch [6.4mm] thick. Scroll way down to see our mechanical power leaf
brake machines that have capacity to bend steel up to 3/4" thick.
With the push of a button, these metal folding machines will clamp the
metal in place and use a hinged apron leaf to fold the metal until the
desired angle is reached. They are easier to operate than press brakes
and thought to be safer. The metal bending is very similar to a Sheet
Metal Hand Brake Machine but with push buttons to tell the hydraulic
cylinders to do all the work. A box and pan capable version is available
to avoid having the bent sides hit against the clamping bar when the
3rd and 4th sides of a box shape are being bent. This is done by removing
a clamping bar "finger" at each end of the box since the clamping
bar is divided up into many assemblies called "fingers". An
insert bar is used to form close offset ("zig-zag") bends.
Basic
Instructions: Turn the handwheel to set the back gauge to the bend
distance. Step on the foot switch to open the clamping bar, insert the
metal against the back gauge, set the dial to the angle you want (or
leave it at 90 degrees), step on the other foot switch to close the
clamping bar, push the bend button and you are done.
Production Instructions: Insert the metal against the back gauge,
push the complete cycle button, and you are done because the machine
will automatically clamp the metal, bend the metal and unclamp. It helps
to have a material table and a finished parts table.
Click for a chart of tensile strengths
for aluminum and stainless steel to compare with mild steel. Click
for a Bend Radius Chart for aluminum and stainless
steel
HYDRAULIC POWERED METAL FOLDING MACHINES
A
standard metal folding machine needs no die changes. The machine bed
supports the sheet metal, not the worker. This makes it less labor
intensive than a press brake and therefore is great for short-run,
and just-in-time metal bending jobs. Extra thick aluminum sheet metal
can be bent. Powerful bends can be made in 10 gauge steel up to 8
feet long. Huge sheet metal panels up to 14 feet long can be bent!
Chicago
Dreis & Krump adds hydraulic power with push buttons and foot
pedals to convert its famous sheet metal hand brake machines into
very productive metal folding machines. You can save time, money and
your back with the push button hydraulic power. Two man jobs become
one man jobs. They are so easy to operate. A simple to use bend angle
adjustment dial completely eliminates the need for tooling and related
time consuming setups. This machine can also form your coated or polished
metal without a scratch. These durable, labor saving, high performance
work horses are totally self contained. They will accurately bend
standard or special design forms and can even make 1/4" reverse
bends on light gauge steel with the optional 1/4" insert bar.
Click
to see video of the machine
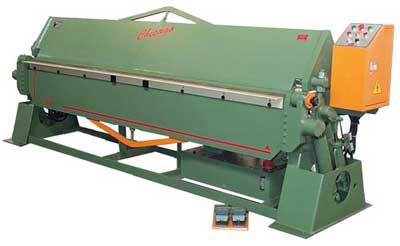
STANDARD HYDRAULIC METAL FOLDING BRAKE
MACHINE
STANDARD EQUIPMENT on each hydraulic powered metal
bending brake machine:
Removable Nose
Bar
Bolted Bottom Bar
Compact Hydraulic Power Unit
Angle Bar
Insert Bar
Oil Level Sight Gauge
Electric Foot
Switch - Clamps and unclamps Top Leaf. Allows operator mobility
when loading and unloading material.
Bend Angle Dial Adjustment - Adjustable cam and scale that
read in degrees, actuates an electric limit switch for bend angle
control and repeatability of bends.
Material Thickness Dial Adjustment - Reference scale for speedier
set up when adjusting clamping pressure.
Back Gauge - 25 1/2" travel, rack and pinion type with
hand wheel adjustment on right side of machine. Inch/Cm scales. This
back gauge will both measure and square up your metal..
Inch Control - Bending leaf up/down pushbuttons allow complete
operator control of the bending leaf motion.
Automatic Cycle - Actuating the "Automatic Pushbutton"
clamps the top leaf, raises the bending leaf to the preset bend angle
dial adjustment setting, lowers the bending leaf, unclamps the top
leaf.
OPTIONS AVAILABLE:
• Insert Bar - 1/4 inch (for closer offset bends)
• Radius Formers - for forming gutters, mouldings, and prototypes
from thin sheet metal.
• Electronic push button operated Back Gauge with digital readout
(see directly below).
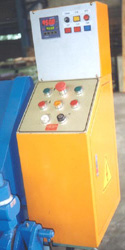
Photos of digital readout back gauge system option
HYDRAULIC METAL BENDING BOX & PAN BRAKE MACHINE
With fingers for box and pan type and optional radius forming to
depth of up to 6"
Click
to see video of this hydraulic metal bending machine
Click
for our instructions how
to make a box out of sheet metal.
STANDARD EQUIPMENT on each hydraulic powered metal bending brake
machine:
Removable Nose Bar
Bolted Bottom Bar
Compact Hydraulic Power Unit
Angle Bar
Insert Bar
Oil Level Sight Gauge
Electric Foot Switch - Clamps and unclamps Top Leaf. Allows
operator mobility when loading and unloading material.
Bend Angle Dial Adjustment - Adjustable cam and scale that
read in degrees, actuates an electric limit switch for bend angle
control and repeatability of bends.
Material Thickness Dial Adjustment - Reference scale for
speedier set up when adjusting clamping pressure.
Back Gauge - 25 1/2" travel, rack and pinion type with
hand wheel adjustment on right side of machine. Inch/Cm scales.
This back gauge will both measure and square up your metal..
Inch Control - Bending leaf up/down pushbuttons allow complete
operator control of the bending leaf motion.
Automatic Cycle - Actuating the "Automatic Pushbutton"
clamps the top leaf, raises the bending leaf to the preset bend
angle dial adjustment setting, lowers the bending leaf, unclamps
the top leaf.
OPTIONS AVAILABLE:
• Radius Nose Bars up to 1.5" radius (great for aluminum aircraft
work) -see picture below.
• Extension Fingers (to form rigid inside corners with a return
flange across the top) -see below.
• Open End Fingers (to form tubes of triangular, square, rectangular,
or tapered shape) -see below.
• Insert Bar - 1/4 inch (for closer offset bends)
• Radius Formers - for forming gutters, mouldings, and prototypes
from thin sheet metal.
• Electronic push button operated Back Gauge with digital readout
(see directly below).
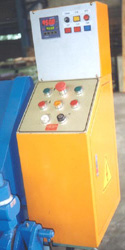
Photos of digital
readout back gauge system option
Model
Number
|
Bending
Length
|
CAPACITY
|
Motor
HP
|
Weight
Lbs.
|
Mild
Steel
|
Stainless
Steel
|
|
48"
|
12
gauge
(.105")
|
16
gauge
(.06")
|
2
|
2800
|
|
72"
|
12
gauge
(.105")
|
16
gauge
(.06")
|
2
|
3300
|
|
96"
|
12
gauge
(.105")
|
16
gauge
(.06")
|
3
|
4700
|
|
96"
|
10
gauge
(.135")
|
14
gauge
(.075")
|
5
|
6400
|
|
120"
|
14
gauge
(.075")
|
18
gauge
(.048")
|
3
|
5500
|
MODEL
|
Width and number of 6 inch long Fingers
|
3"
|
4"
|
5"
|
6"
|
Total
|
HBPU 412-6
|
5
|
2
|
5
|
0
|
12
|
HBPU 612-6
|
5
|
4
|
7
|
1
|
17
|
HBPU 810-6
|
5
|
6
|
9
|
2
|
22
|
HBPU 812-6
|
5
|
6
|
9
|
2
|
22
|
HBPU 1014-6
|
6
|
10
|
10
|
2
|
28
|
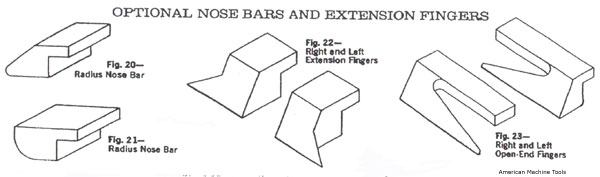
Optional
Radius Nose Bars are available for bending your metal around a radius,
which is useful for bending aircraft aluminum. Extension Fingers
are used to form inside corners with a return flange across the
top. Open End Fingers are used to form tubes of triangular, square,
rectangular, or tapered shape.
HYDRAULIC POWERED METAL
BENDING MACHINE
capable of bending 3/16 or 1/4 thick steel up to 10 feet long
|
Buy
it equipped with NC Controls for back gage and bend angle. This
is the next best thing to owning a Press Brake but without the
high price or tool changes. The Chicago Hydraulic Powered Leaf
Brake will bend up to 1/4 inch thick steel but it can also bend
sheet metal without changing the tooling! Model HBP is designed
to make box shapes and pan shapes up to 6 inches deep. This
machine is easy to use because it works similar to a hand brake
machine.
Click
to see video of the machine
|
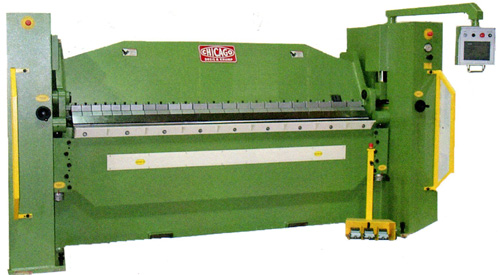
Features:
Adustable clamping pressure, adjustable open height, bending
leaf gap adjustment, hand wheel operated manual rack & pinion
type back gauge with positioning bar or optional numerically
controlled back gauge with digital readout. Bend position and
bend angle can be stored and changed in the NC control panel.
The box/pan capable version has removeable fingers. Minimum
reverse bend is 1.18" on 3/16" capacity machine. Minimum
reverse bend is 1.37" on 1/4" capacity machine. |
Model
Number
|
Bend
Length
|
Thickness Capacity
|
Motor
HP
|
Weight
Lbs.
|
Mild Steel
|
Stainless
|
HSB-8187
Click
to Request this Quote |
97"
|
3/16
(.187")
|
11
gauge
(.105")
|
7.5
|
10,500
|
HSB-8250
Click
to Request this Quote |
97"
|
1/4
(.250")
|
3/16
(.187")
|
10
|
13,200
|
HSB-10187
Click
to Request this Quote |
121"
|
3/16
(.187")
|
11
gauge
(.105")
|
7.5
|
11,400
|
HSB-10250
Click
to Request this Quote |
121"
|
1/4
(.250")
|
3/16
(.187")
|
10
|
14,900
|
Below
are the same Machines but they built with box/pan making capability
|
HBP-6187-6
Click
to Request this Quote |
73"
|
3/16
(.187")
|
11
gauge
(.105")
|
7.5
|
7,000
|
HBP-6250-6
Click
to Request this Quote |
73"
|
1/4
(.250")
|
3/16
(.187")
|
10
|
8,160
|
HBP-8187-6
Click
to Request this Quote |
97"
|
3/16
(.187")
|
11
gauge
(.105")
|
7.5
|
11,200
|
HBP-8250-6
Click
to Request this Quote |
97"
|
1/4
(.250")
|
3/16
(.187")
|
10
|
13,600
|
HBP-10187-6
Click
to Request this Quote |
121"
|
3/16
(.187")
|
11
gauge
(.105")
|
7.5
|
12,100
|
HBP-10250-6
Click
to Request this Quote |
121"
|
1/4
(.250")
|
3/16
(.187")
|
10
|
15,600
|
Click to for our sheet
metal Shear machines
|